Cross roller bearing is a special type of bearing with inner ring split and outer ring rotating. Because the separated inner or outer ring is fixed together with the cross roller shaft ring to prevent separation from each other after being loaded into the roller and spacer, it is easy to operate when installing the cross roller shaft ring. Because the rollers are cross arranged, only one set of cross roller shaft rings can withstand loads in all directions, and the rigidity is increased by 3 to 4 times compared with traditional models. At the same time, because the inner ring or outer ring of the cross roller bearing is two separate structures, the bearing clearance can be adjusted, even if the preload is applied, it can also obtain high-precision rotating motion.
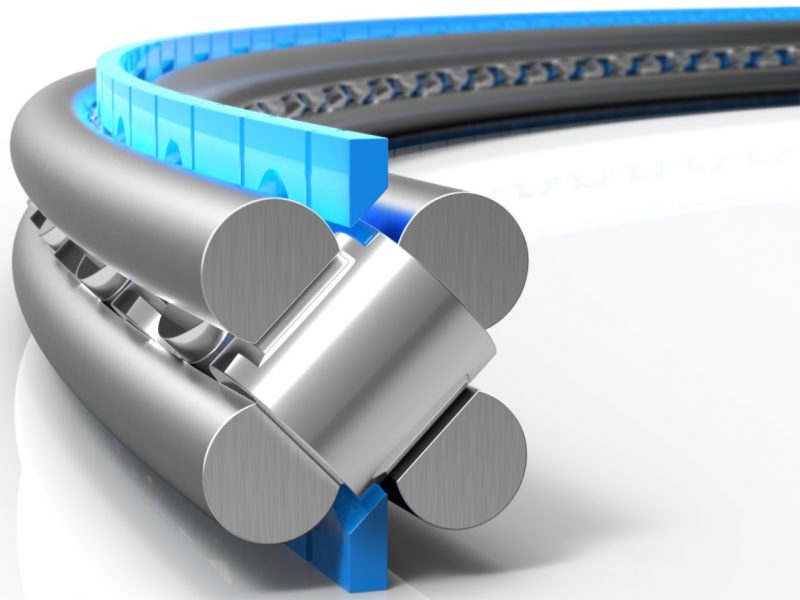
The rollers of cross roller bearings are arranged at right angles to each other between the inner and outer wheels. They can withstand loads from all directions (such as axial, thrust or momentum loads) at the same time. Because the roller is in linear contact with the track surface, the possibility of bearing elastic deformation under load is very small. This type of bearing is widely used in industrial automatic robots, work machinery and medical facilities, etc., where high rigidity, tight and high speed can still ensure accuracy.
In cross roller bearings, because the cylindrical rollers are arranged vertically to each other through the spacer, a cross roller bearing can withstand radial load, axial load and torque load in all directions. The size of the inside and outside the circle is a minimum of miniaturization, especially extremely thin type is close to the limit of small size, and high rigidity, so the most suitable for industrial robot joint department or rotate department, machining center of rotary worktable, manipulator rotate, precision rotary worktable, medical machine, meter, IC manufacturing devices use.
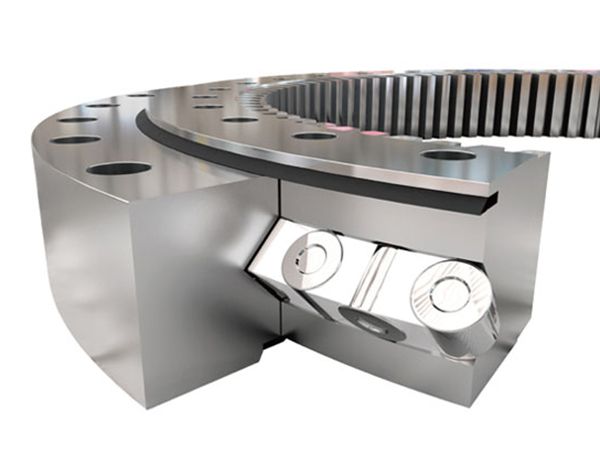
What is the “cross” of roller bearing
The cross roller bearing is easy to operate when installing the cross roller shaft ring because the inner or outer ring which is divided is fixed together with the cross roller shaft ring to prevent separation from each other after being loaded into the roller and spacer. Because the roller is cross arranged, so only 1 set of cross roller shaft ring can bear the load in all directions, compared with the traditional model, the rigidity is improved 3~4 times. At the same time, because the inner ring or outer ring of the cross roller bearing is two separate structures, the bearing clearance can be adjusted, even if the preload is applied, it can also obtain high-precision rotating motion.
Features and advantages of cross roller bearings:
1, With excellent rotation accuracy
The internal structure of cross roller bearing adopts 90° vertical cross arrangement of rollers.
The rollers are equipped with a spacer or isolation block to prevent the rollers from rubbing each other. In addition, there will be no roller contact phenomenon or lock phenomenon; At the same time, because the inner and outer rings are divided structure, the clearance can be adjusted, even if the preload is applied, also can obtain high precision rotary motion.
2. Simplify operation and installation
The outer or inner ring, which is divided into two parts, is fixed together after the roller and retainer are loaded, so the operation of installation is very simple.
3, Bear large axial and radial load
The rollers are arranged perpendicular to each other by spacer on a 90° V-groove rolling surface.
4, Greatly save installation space
The size of the inner and outer ring of the cross roller bearing is minimized, especially the ultra-thin structure is close to the limit of small size, and has high rigidity. So the most suitable for industrial robot joints or rotating parts, machining center of the rotary table, manipulator rotating part, precision rotary table, medical instruments, measuring instruments, IC manufacturing devices and a wide range of uses.
5. High speed capacity
6. Reduce shaft length and machining cost, thermal expansion leads to limited changes in geometric dimensions
7. Nylon separator, low moment of inertia, low starting torque, easy to control Angle division
8. Optimized preload, large stiffness, high precision of guide roller operation
9. Carburized carbon steel provides excellent impact resistance and surface wear resistance
10. Simple but well lubricated
Features and advantages of cross roller bearing
1. Cross roller shaft has the characteristics of high rigidity, accuracy and easy installation. Mounting holes allow them to be quickly fixed to components. Cylindrical roller of this type .Also equipped with isolation block.
2. Cross roller bearings have strong, non-detachable inner and outer ring structures, which can easily achieve high stiffness and high accuracy without being affected by surrounding structures. Bearing optimum for medium to high speeds, bearings are fitted with isolation blocks between cylindrical rollers to provide smooth rotation.
3. The outer diameter of cross roller bearings is small and the width is narrow. If you need high performance and take up less space, you can also choose to use cross roller bearings.
Because the cross roller bearing is divided into two parts of the outer ring or inner ring, after loading the roller and reholder, is fixed together, so the installation operation is very simple, and the high precision characteristics of the cross roller bearing, the accuracy can reach P4/P2 level, smaller volume, so that the host more space saving.
THREE-ROW ROLLER SLEWING BEARINGS
CROSS ROLLER BEARING