In the current transmission mechanism, the application range of slewing drive is very wide, including the application of products such as high-altitude lifting platforms, fire trucks, marine cranes, and log transfer machines. In a complex application environment, the slewing drive device will inevitably fail due to various reasons. The editor below has sorted out some common faults and solutions of the slewing drive device and hopes to be helpful to everyone.
Common causes of failures of slewing drive devices
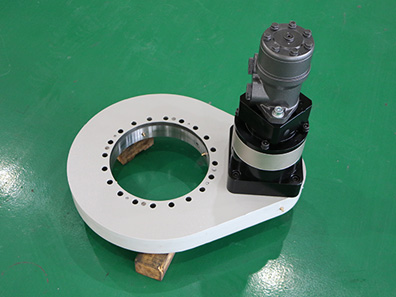
1. Rotary drive string shaft
(1) Shaft tandem caused by broken teeth causing the input shaft to lose its axial restraining force;
(2) The slewing drive driven gear is not tightly fastened to the shaft, resulting in insufficient bearing interference, resulting in a series of shafts, and the steering problem of the slewing drive is affected;
(3) Gear machining deflection;
(4) Gear helix angle error;
(5) Tooth thickness error, uneven wear of tooth surface and premature wear, deformation of tooth back.
The rotary drive oil temperature is too high
(1) The lubricating oil used by the rotary drive is unqualified or has been used for too long;
(2) Too much lubricating oil is used in the rotary drive;
(3) Damage to the slewing drive components, including severe pitting of gears, broken teeth, damage to the bearing cage, inner and outer rings, balls, as well as bearing seizure or severe shaft deformation;
(4) The outside of the rotary drive is covered by debris or dust. When things are piled around or the surface of the machine body has not been cleaned for a long time, the cover of debris or dust may cause incomplete heat dissipation of the reducer and increase the oil temperature;
(5) The cooling device fails or is blocked. If the cooling device is blocked or the cooling device is broken due to long-term work without cleaning the internal pipeline, it will cause the temperature of the rotary drive oil to rise;
(6) Overload operation of rotary drive.
Oil leakage of rotary drive
The oil leakage of the slewing drive: the driving shaft seal ring, the driven shaft seal ring, the slewing drive box, the sight hole cover, the oil drain hole at the bottom, and the oil leakage of the breather. Possible reasons include the fixing bolts are not tightened; there is iron filings on the joint box surface and the closure is not tight; the rotary drive housing is deformed and does not fit tightly and leaks oil; or the ventilator has too much oil.
The slewing drive is overheated or there is noise in the bearing part
(1) Insufficient lubricating oil. When the lubrication oil level is insufficient or the reducer cannot reach a reasonable height due to oil leakage, it may cause high temperature or noise in the bearing part of the reducer;
(2) The bearing cap or seal part is rubbed. When the bearing cover or the sealing part and the connecting part are worn due to improper installation, improper bearing cover or long-term use, the bearing temperature of the reducer may be high or there may be noise;
(3) The bearing is damaged or worn. This item mainly includes damage to the cage of the bearing, wear or deformation of the inner and outer rings, wear or fall of the balls, these reasons will make the reducer unable to work normally;
(4) The bearing clearance is too large or too small. The above symptoms may be caused when the gap between the ball of the reducer bearing and the inner and outer rings, the gap between the bearing inner ring and the shaft, and the gap between the bearing and the end cover increase due to long-term use;
(5) The key handle of the helical gear is loose. The looseness of the helical gear key handle will cause the lack of tight fit between the gear and the shaft, resulting in overheating or noise in the bearing;
Large vibration of the rotary drive body
The possible reasons for the vibration of the slewing drive body include: the anchor screw is loose; the coupler is damaged; the motor screw is loose; the bearing is severely worn; the gear is damaged; the shaft is deformed and out of balance. These conditions may be due to loose screws or coupler failures, bearing wear and other reasons caused by long-term operation.
The bearing of the slewing drive device is broken
The slewing drive bearing cracks mainly occur in the driving shaft bearing. The main reason is that when the driving shaft moves, axial sliding will occur between the bearing inner ring and the rollers, causing the bearing inner ring to move axially, causing the inner bearing rollers to move first. Damage to the bearing.
Damage to the slewing drive gear
Rotary drives have different reasons for broken teeth, gear pitting, spalling, and wear. It can be roughly divided into insufficient contact fatigue strength of the gear; gear material defects, poor precision, inadequate lubrication, impurities in the lubricating oil, and errors in the center distance of the gears.
The slewing drive device has abnormal noise
Possible causes The reducer is overloaded; the load of the working machine is unbalanced; the lubricating oil is deteriorated; the gear tooth surface is worn or the manufacturing quality is poor; the bearing clearance is too large or too small; there is adhesion on the tooth surface; there is debris in the box.
After understanding the causes of common failures of the slewing drive device, the editor briefly introduces the repair methods of the slewing drive device failure. You can check the fault according to the specific situation. If you can’t solve it by yourself, you still need to contact the manufacturer for repair.
Solutions to common failures of slewing drive devices
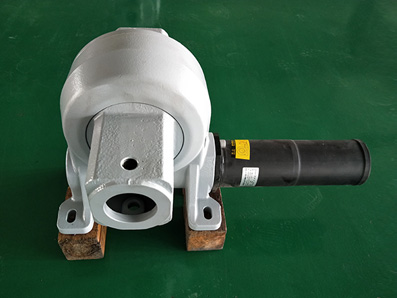
1. Rotary drive string shaft
It can improve the strength and manufacturing accuracy of the gear, and reduce the roughness value of the gear and shaft. Improving the installation accuracy and tightness of the driven gear and the shaft is mainly to achieve a reasonable interference fit.
2. The rotary drive oil temperature is too high
(1) The staff can perform a detailed inspection on the actual load of the slewing drive and adjust it to the specified value, or it can be replaced with a larger power slewing drive.
(2) Use lubricating oil to remove excess oil in strict accordance with the prescribed amount of oil; or replace the lubricating oil.
(3) Remove the debris and dust around the rotary drive, replace the cooling device to remove the blockage.
3. Oil leakage of rotary drive
(1) The sealing ring gland adopts an open structure or an easily disassembled structure.
(2) Install gaskets and fastening bolts on the sight hole cover.
(3) The oil return hole at the input shaft bearing should be appropriately enlarged.
(4) Replace the deformed drive housing.
(5) Correctly install and correct the oil level of the ventilator.
(6) An annular oil groove is cast or machined on the box surface of the rotary drive base, and there are multiple oil return holes communicating with the annular oil groove. When the reducer is working, once the oil penetrates into the joint box surface, it will enter the annular oil groove, and then flow into the oil tank through the oil return hole, and the lubricating oil will not leak along the box surface to the outside of the reducer housing.
(7) Apply a layer of sealant (such as D05 silicone rubber sealant) on the surface of the box to effectively prevent oil leakage at the surface of the box.
(8) Improve the ventilation cap and inspection hole cover. The internal pressure of the reducer is greater than the external atmospheric pressure is one of the main reasons for oil leakage. If you try to balance the pressure inside and outside the machine, oil leakage can be prevented. Although the reducer has a vent cap, the vent hole is too small, and it is easy to be blocked by dust and oil. Moreover, the inspection hole cover must be opened every time the oil is refueled. Once opened, the possibility of oil leakage will increase once, so that the original place does not leak. Leaks also occurred. The vent hole can be enlarged to equalize the pressure inside and outside.
4. The slewing drive is overheated or there is noise in the bearing part
(1) Check the rotary drive oil level and add lubricating oil;
(2) Tighten the bolts of the bearing and the connecting part, and check the installation of the seal;
(3) Check the bearing and replace it immediately if it is damaged;
(4) If the clearance is not suitable, adjust the bearing clearance, and replace the bearing if it cannot be adjusted;
(5) If the key handle of the helical gear is loose, send it for repair in time;
5. The vibration of the rotating drive body is large
The fault can be eliminated by tightening the foot bolts and the loose screws of the motor; repairing the coupler; replacing the bearing; replacing the gear.
6. The slewing drive bearing is broken
Increase the interference between the inner ring and the shaft, or add a retaining ring on the outer side of the inner ring of the bearing to prevent axial movement.
7. Rotary drive gear damage
Gear damage can be strengthened or the viscosity of the regular lubricant can be used to reduce the loss of lubricant and prevent rust. Clean the gear to keep the surface free of impurities, replace the gear that cannot be repaired, and pay attention to daily maintenance.
8. The slewing drive device has abnormal noise
When there is abnormal noise, you can replace the new lubricant to adjust the bearing gap, check the bearing and do the cleaning work, or replace the new parts in time.
The above is the sorting and summary of the common failure causes and solutions of the rotary drive device. I hope it will be helpful to everyone.